Après des décennies de standardisation et alors que la société de consommation prône une économie linéaire, la culture maker (c’est-à-dire du « faire soi-même ») émerge et se fabrique une place sur mesure en impression 3D. Avec des outils de fabrication accessibles, une documentation open-source et des lieux dédiés à la création, le message est fort : ta seule limite est ton imagination !
Un conte philosophique relate la réponse décalée d’un sculpteur à une personne admirant son œuvre et qui lui demande « Comment faites-vous pour que cette girafe taillée dans un bloc de pierre soit si réaliste ? » Le sculpteur lui rétorque simplement « C’est simple, je prends un bloc de pierre et j’enlève tout ce qu’il y a autour de la girafe ! » En une phrase, ce sculpteur décrit un procédé de fabrication soustractive. A partir d’une forme pleine (le bloc de pierre), il convient d’enlever des morceaux de matière pour créer une nouvelle pièce (la sculpture de la girafe). Ces procédés soustractifs engendrent une perte de matière, certaines parties de la forme pleine sont délaissées car elles ne font pas partie du produit final.
Mais si le sculpteur possédait une imprimante 3D, il aurait pu répondre « C’est simple, la machine dépose des couches de matières ayant directement la forme de la girafe ! » Cette version a perdu le caractère humoristique de la première, mais dans ce second récit, l’artiste n’utilise que la ressource strictement nécessaire à la réalisation de l’objet. Il s’agit alors de fabrication additive, où l’objet final est créé par dépôts successifs de matière jusqu’à l’obtention de la forme désirée. Les procédés de fabrication additive sont nombreux – l’impression 3D en est l’emblème le plus médiatisé – et offrent davantage de possibilités pour la fabrication de pièces complexes.
Avant d’exposer le fonctionnement des principales techniques de fabrication additive et de leurs applications, une entrée en matière sur-mesure par l’impression 3D est prévue.
Imprime moi un mouton
Une figurine à votre égérie, le morceau manquant d’une tasse brisée, ou pourquoi pas un vêtement sur mesure en plastique de maïs… autant de projets de création d’objets sans doute introuvables dans le commerce – à moins, pour la figurine, d’être une grande Diva ! Les amateurs et amatrices de projets de fabrication ou DIY (do it yourself – fais-le toi même) dépassent les limites de la consommation standardisée en adoptant la culture maker. Il s’agit de promouvoir le réflexe de concevoir soi-même ses propres objets en fonction de ses besoins et en utilisant le moins de ressources possible, favorisant ainsi une économie circulaire, plutôt que linéaire.
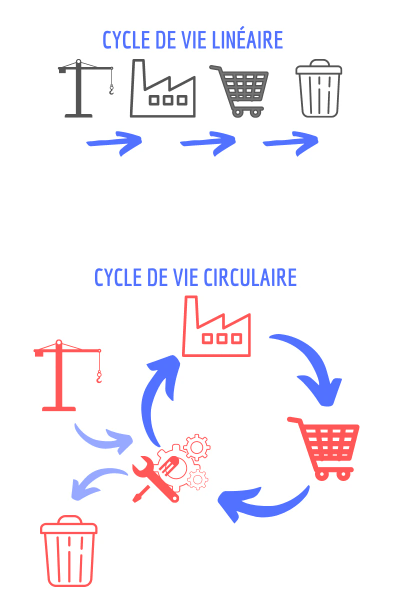
Schéma comparatif des chaînes de consommation linéaire et circulaire. Dans le premier cas, les ressources sont extraites pour fabriquer un objet, l’objet est utilisé puis jeté. Pour concevoir un nouvel objet, de nouvelles ressources sont extraites. Alors que l’économie circulaire consiste en la réutilisation des ressources issues d’un objet en fin de vie afin de ne pas extraire de nouvelles ressources.
La communauté maker est vaste, conviviale et internationale et de nombreux lieux dédiés à la création et accueillant les novices aussi bien que les adeptes, fleurissent et se remplissent de toutes sortes de machines et d’outils en accès libre et mutualisés (les FabLabs sont un exemple de ces lieux). Parmi ces machines et outils, une nouvelle venue aux aspects futuristes est presque aussitôt placée sur un piédestal (qu’elle aurait elle-même réalisé ?) : l’imprimante 3D, existant pourtant depuis les années 1980.
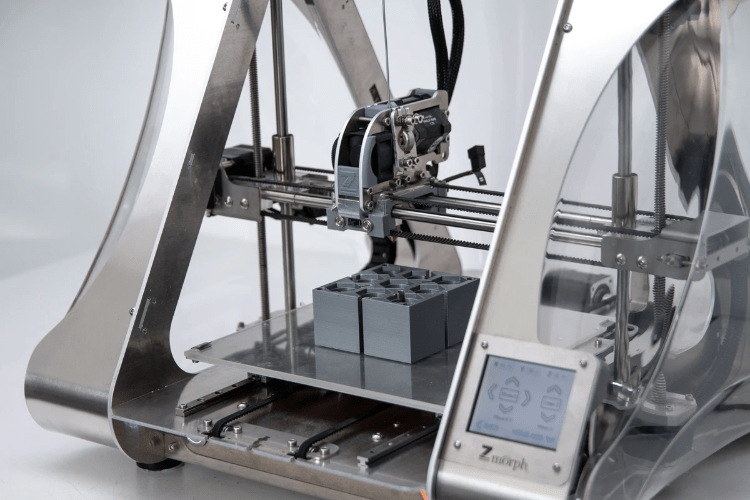
Elle s’est imposée sur le marché de la création, bénéficiant de l’essor de la conception d’objets non-standardisés et personnalisés. Tout d’abord, un modèle 3D est à importer dans le logiciel de l’imprimante. Celui-ci peut être dessiné à partir d’un logiciel spécifique ou issu d’une banque de modèles en libre accès (certaines imprimantes peuvent même scanner un objet à répliquer). Ensuite, l’imprimante est paramétrée pour ajuster l’épaisseur des couches par exemple et la bobine de matériau est insérée. Enfin, la fabrication du modèle 3D commence : la tête d’impression fait fondre le filament de matière et se déplace au-dessus d’un plateau pour déposer le filament aux positions correspondant à celles du modèle 3D.
Cette technologie a le potentiel de bouleverser la manière de produire, car son usage n’est pas réservé à l’industrie ou la production de masse. Le procédé peut justement être appréhendé par les particuliers, qui peuvent alors avoir le loisir de réaliser cette fameuse figure à leur égérie. Plus largement, l’impact de l’accès du grand public à cette technologie est la possibilité de proposer de réelles innovations – telles qu’un nouveau type de textile, des becs de saxophones adaptés à la morphologie du musicien ou de la musicienne ou encore du matériel sportif sur-mesure.
Déposer, solidifier, agglomérer
A présent, l’imagination ne semble plus être une limite et la fabrication additive permet de n’utiliser que la matière utile pour l’objet à fabriquer. Justement, quelles sont ces matières ? Les bobines insérées dans les imprimantes 3D destinées aux particuliers étaient à l’origine composées de plastique conventionnel (issu de la pétrochimie ou recyclé à partir d’anciens objets imprimés), puis ont été remplacées par des bobines de filaments en matière végétale. Mais au-delà des objets en plastique, la fabrication additive permet d’envisager des créations en béton par exemple pour construire des habitations, mais aussi en métal dans l’automobile ou en tissus humains. En effet, des applications biomédicales existent et admettent la fabrication de prothèses, d’implants ou d’outils chirurgicaux adaptés à un type d’opération.
Outre la capacité à limiter les pertes de matière, la fabrication additive permet plus d’adaptabilité de la chaîne de production, au niveau industriel, dans le cas d’un changement sur la pièce à fabriquer et moins de logistique que dans un processus de fabrication soustractive. Il existe trois catégories principales de procédés de fabrication additive.
Tout d’abord le dépôt de matière - principalement évoqué dans cet article - qui est flexible et accessible mais nécessite d’adapter la tête d’impression au matériau utilisé et au type d’objet à réaliser (en fonction de son volume). Par exemple, l’impression 3D d’un bâtiment en béton nécessite une logistique différente que la fabrication d’un objet décoratif aux motifs complexes. Un autre procédé est la solidification par la lumière (ou stéréolithographie) qui consiste en la solidification d’un liquide photosensible par un rayon laser. Le logiciel de cette machine transforme le modèle 3D en une série d’images 2D décrivant chaque couche de l’objet à fabriquer. Le liquide est contenu dans un réservoir cubique équipé d’une plateforme pouvant se déplacer verticalement pour présenter au laser une nouvelle couche à solidifier, après chacun de ses passages. Pour gagner en précision, le liquide peut également être remplacé par une poudre à solidifier par frittage laser suivant le même processus. Enfin, la poudre peut être utilisée par le dernier procédé de fabrication, d’agglomération par collage. Il s’agit de déposer de fines couches de poudre sur une plateforme. Cette fois la tête d’impression ne projette pas de rayon laser, mais des gouttes de glu colorée afin d’agglomérer les grains de poudre d’après le modèle 3D de l’objet à créer. Ce dernier procédé est moins coûteux (à échelle industrielle) mais un traitement des pièces produites est indispensable pour assurer leur solidité.
Finalement, la fabrication additive offre l’opportunité de concevoir des objets en minimisant la perte de matière et en s’affranchissant des limites imposées par la production standardisée de masse. Malgré les compromis à réaliser parfois entre le panel de matériaux, le prix ou la complexité de la fabrication additive, cette technique est adaptée à la production industrielle aussi bien qu’à une échelle individuelle ou artisanale. Les amateurs et amatrices de création se sont d’ailleurs emparés du procédé grâce à l’imprimante 3D notamment, qui permet une vaste liberté et qui rend la fabrication accessible et personnalisable.
Pour en savoir plus
Article paru dans Je Science donc J'écris n°29 - Janvier 2022